Plastic Injection Moulding Delivers A Lifesaver
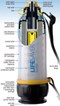
Riverside Business Park, UK - The UK's leading rapid plastic injection mould making facility, Omega Plastics, has completed the first stage of an innovation-led project to deliver a potentially life-saving device to the market.
Omega's latest inventor-led project is the development of the Lifesaver filtering bottle, an ingenious idea from Suffolk-based entrepreneur Michael Pritchard. Omega has taken its 14 components from design concept, through prototype development, to manufacture, assembly and packaging. Able to filter contaminated water into water of drinkable quality, this bottle will, quite literally, save lives.
The Tsunami of 2004 and Hurricane Katrina in 2005 drove Michael Pritchard to introduce a product which, if not able to prevent, would have certainly have reduced, the need for clean water to be provided to the affected areas. The Lifesaver bottle has an all-in-one filtration system which works to remove viruses, bacteria, parasites, fungi and all waterbourne pathogens, and was voted Best Technological Development for Future Soldier System Enhancement at the Soldier Technology Awards 2007.
Mr Pritchard employed the services of Omega Plastics after spending some considerable time working on the filtration process, and some less productive time with some design concepts which never really materialised prior to his involvement with Omega.
"It took a little while and some very frustrating rapid prototypes, but eventually I did it. Once I had met with the Omega guys and discussed what my intentions were, they became almost as enthusiastic about the idea as I was, and given my investment at that point, it was heartening to have a supplier on board who was prepared to work with my product and advise of areas of improvement, which ultimately reduced both the cost and the delivery time of the mass-produced plastic product, without impinging on its functionality."
All 14 tools, in both aluminium and P20 steel, were manufactured in the Omega facility over a period of 6 weeks, followed by a period of stringent testing and engineering development lasting a further 4 weeks.
Working with key suppliers such as E3d Design, Albis and Data Supplies, Omega has now commenced the next stage of its production volume campaign, which will ultimately lead to the introduction of another 4 injection moulding machines to a bespoke facility, with talks already underway with Negri Bossi, Sandretto and Fanuc.
For more information, please visit www.lifesaversystems.com
These concepts serve a wide spectrum of markets, from the office to the military. Dave finds it heartening that the UK can still generate so many good ideas, and, coupled with the protection of intellectual property, believes that this is key to maintaining business generation within the UK
In addition to the above, Omega has a strong portfolio of existing customers who have a genuine requirement for rapidly manufactured high quality tooling for testing, or low-volume runs of their own stand-alone proven products, something that is essential to the development of company.
All of these factors have resulted in a dramatic 20% rise in Omega's enquiry levels over the last six months. The enquiry conversion factor has also increased, and Omega is winning more work than ever before. Six months ago, the enquiry conversion rate stood at 10-11%, now it is over 20%. Dave puts this down to a high level of service, continued investment in machinery (in particular 2 new Deckel Maho Gildermeister CNC machine centres), and a more targeted marketing approach, through search engine optimization for Omega's website. Investment in these areas over the last 12 months has been in excess of £200,000, and it doesn't stop there.
In a bid to provide an even quicker service to its customers, Omega has moved its factory closer to its employees. Dave explains:
"We previously occupied 13,000 sq ft premises in Team Valley, Tyne & Wear, whereas 80% of our employees live in Northumberland, which meant they could take an hour to get to work. This may not be a concern to some companies, but to us, cutting this travelling time is vital to offering a reliable, reactive service to our customers, which will be further improved in the coming months, following our move to a brand new facility in Northumberland."
SOURCE: Omega Plastics