New Highly-Toughened Nylon 6 From Clariant: Easier To Color And Process; Better Surface Finish
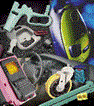
Millington, MD A new family of Nylon 6 compounds from Clariant Masterbatches North America offers industrial designers highly-toughened properties, easier processing, improved surface finish, reduced moisture absorption, more color options and competitive pricing.
Until now, designers looking for a highly-toughened Nylon (polyamide) had to make some difficult choices… specify a toughened Nylon 6,6 that was difficult to process and probably over-engineered for many applications, or choose one of the few impact-modified Nylon 6 compounds currently available and make do with limited colorability, inferior surface finish, less-than-ideal properties and high costs.
"These new Nylon 6 compounds have properties that are similar to impact-modified Nylon 6,6, but they offer all the benefits of Nylon 6 in the molded part," explains Bill Blasius, Director of Technology – North America for Clariant Masterbatches. Property data for unfilled versions includes notched Izod impact of 16 ft-lb/in, which is many times higher than standard modified Nylon 6. They also deliver tensile strength of 7,000 psi, flexural modulus of 280,000 psi, and flexural strength of 11,000 psi. Typical processing temperatures are 470 to 530°F – very similar to standard unmodified Nylon 6.
The new compounds are targeted at applications in lawn & garden, power tools, furniture, sporting goods, electrical products and even interior automotive components. "A lot of these applications require more toughness than conventional Nylon 6 can deliver," adds Blasius, "but impact-modified Nylon 6,6 is really over-engineered – and over-priced – for almost anything except high-temperature applications like under-the-hood automotive parts. In addition, our new highly-toughened Nylon 6 compounds have substantially lower viscosity than toughened 6,6 resins, so they can be processed through pin gates and can readily fill thin-walled sections and still provide a good surface finish."
Produced in the Clariant Masterbatches Specialty Compounding plant in Millington, MD, and marketed regionally, these standard products form a platform from which custom grades can be produced using the same toughening architecture. Other options include glass or mineral reinforcement, flame-retardance, UV and wear additives. These materials can even be produced in small lots and special colors.
In fact, colorability is another major advantage of the new highly-toughened compounds. Blasius notes that other similar materials on the market use copolymer additives that result in opaque materials. These, he says are "notoriously difficult and expensive to color." The new Clariant materials, on the other hand, use a different, proprietary combination of additives that actually result in a translucent material that is much more receptive to color and can deliver excellent contact clarity. Compared to standard toughened Nylon 6,6, the impact modifier melts more readily, so colors that would degrade at higher processing temperatures can be used in the new Clariant Nylon 6. This opens up a much broader palette for designers to choose from. Plus, the new compounds require less color to achieve the desired effect, so they maintain their physical properties better and can be very cost-competitive, Blasius says.
SOURCE: Clariant Masterbatches Specialty Compounding