Do I Have Enough Cooling Lines In My Mold?
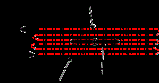
By Douglas M. Bryce
OVERVIEW
Once the molten plastic
is injected into the cavity image, it is allowed to stay there, under pressure,
until it has cooled down and solidified enough to be removed from the mold. The
plastic need not be totally cooled, just enough to allow ejection of the
finished product without unacceptable distortion occurring to the plastic. This
cooling is accomplished through the use of a mold temperature control system
that is used to remove heat from the mold and maintain the correct mold
temperature for the specific plastic material and product design being employed.
In the following section we will examine the more common methods used to
accomplish this feat.
* Waterlines
The use of waterlines machined
throughout the mold to allow water to flow through the mold is the most common
method of controlling mold temperature. This is accomplished by drilling holes
(1/8" pipe, 1/4" pipe, and 3/8" pipe are most common) across the
various plates of the mold, as close as possible to the actual molding area of
the cavity sets. (See the following drawing).
Common
Waterline Layout
Because of the accuracy
required, the drilled holes are usually machined using a gun drill or deep
boring tool. Then they are fitted with pipe threads which are used for
connecting nipples, hoses, and/or quick-disconnect fittings. Hoses are connected
to floor-mounted temperature control units, or to water manifolds which are
normally mounted on the molding machine. Regardless of which system or device is
used to maintain mold temperature, it must be emphasized that there should be no
more than a ten (10) degree (F) difference between any two points of the cavity
molding surfaces, either between two points on the same mold half, or between
two points of both mold halves. Any more than 10 degrees (F) difference will
cause excessive stress to be molded into the part and also will result in
unbalanced plastic flow during the injection phase. The excessive stress is
caused by differences in the cooling time required for hotter sections of the
mold. These areas also shrink more than the cooler sections.
- Control Units Versus
Manifolds
Control Units
If floor mounted temperature
control units are used, a single unit should be used for each half of the mold.
This eliminates the practice of using heated water from the first mold half to
try to "cool" the second mold half, as is done when using only one
control unit.
Mold
Temperature Control Unit
The unit has a set point which
is determined by the user. Water is circulated through the unit and heated by
the unit until it meets the desired set point. Then the water simply continues
to circulate until it gets too warm, at which point the unit begins to dump the
heated water and replace it with tap water until the desired temperature is
reached. This process continues as the unit functions to maintain the desired
temperature. The temperature of the circulating water is read through a
thermometer mounted on the unit. Remember that this is only an indication of the
water temperature and NOT the mold temperature. The mold temperature must always
be measured by using a surface pyrometer on the cavity surfaces.
Manifolds
If water manifolds are
utilized, the water flow is manipulated by throttling shutoff valves at the
connection points of the manifold. Each line can be controlled
independently. The mold temperature is determined by the flow of the water
through these valves, but must be measured by a surface pyrometer on the mold
surface itself. In most cases, the manifolds are connected to a source of
chilled water, usually at a temperature of approximately 50 degrees F. The
manifold concept is based on a system that can control the mold temperature once
it is established, but requires a slow and steady buildup as the metal of the
mold absorbs heat from the injected plastic. The manifold system then depends on
the continuous heat of incoming plastic to create a buildup of heat in the mold
to provide the proper molding temperature. Once that temperature is hit, the
manifold system can maintain it. However, this process may take an hour or two
to level out and the molding parameters may have to be adjusted constantly while
that is happening to ensure properly molded parts.. This creates a condition of
having to "tweak" the manifolds during the first hour or so of
production until the mold reaches the intended temperature.
Another problem is that
some molders utilize a colder mold for faster cycles and more profits. In fact,
especially when molding crystalline materials, most parts require a slow cool
down. This normally means a warm mold and long cooling cycles to create the
highest level of physical strength in the final part. Cold molds will negatively
affect the physical properties of a molded part, while warm molds will enhance
those same properties. There are few situations where cold molds should be used.
If manifold systems are in place there is a tendency for the molder to routinely
lower the mold temperatures close to that available from the manifold system,
which is usually around 50 degrees F. This may result in faster cycles, but can
create a major quality problem if not understood and controlled.
-
Laminar Flow Versus Turbulent Flow
There are two different
types of flow that water can experience when traveling through a waterline of a
mold: laminar or turbulent. The following drawing shows the differences between
the two conditions. Both conditions will remove heat from the surrounding mold
metal, but the laminar flow is not nearly as effective as the turbulent flow.
Laminar
Flow Versus Turbulent Flow
Note that in the laminar
flow diagram the water travels in separate layers. The layers nearest the
outside are next to the mold metal and are in direct contact with the heat that
needs to be removed. These layers move slowly (due to friction) and then
transfer some of that heat to the faster moving inner layers. But the very
center layer, which is moving fastest of all, receives no heat at all.
In the turbulent flow
model the water is constantly being tumbled and mixed. All of the water is in
contact with the mold metal at one time or another and all of it is used to
remove heat from the mold metal. This is the desired effect.
Reynolds Number
The creation of turbulence is a
function of flow rate, waterline diameter, water viscosity, water temperature,
and velocity of the water as it travels through the channels. Whether concerning
laminar or turbulent flow, these conditions are characterized by a ratio known
as the Reynolds number. Conditions causing a Reynolds number of 2000 or less
will result in laminar flow. Ideal turbulence is found when conditions create a
Reynolds number of 3500 or more. And, in between exists a transition area that
fluctuates between laminar and turbulent flow.
Determining the existing
Reynolds number can be achieved by using the following formula:
R = 3160 Q / Dn
where
Q = flow rate in gpm
D = diameter of waterline (inches)
n = water viscosity (centistokes), see Table below
Water Temp.(F)
Viscosity (n)
32
1.79
50
1.30
68.4
1.00
100
0.68
150
0.43
212
0.28
Table - Water Viscosity Versus Temperature
The most important answer we
are attempting to find is the gallons per minute (gpm) required to produce a
specific Reynolds number. The gpm is easily variable when all other conditions
are fixed. So let's perform an exercise to make that determination.
First we must know the
temperature of the water entering the mold. We'll use the temperature of 50
degrees F. Then we need to know the diameter of the waterline we are using. If
we use a 1/8 inch pipe diameter, the actual drilled hole opening diameter (water
passage) is 11/32 inch. Because we want to obtain turbulent flow we will use a
specific Reynolds number of 3500 (that's the minimum we should have).
Remember our formulas is:
R = 3160 Q / Dn. By plugging in the
numbers we have established above we arrive at:
3500 = (3160 * Q) / (0.34375 * 1.30)
or
Q = (3500 * 0.34375 * 1.30) / 3160
or
Q = 0.495 gallons per minute
Therefore, a flow rate of 0.495 gpm with water temperature of 50 degrees F, will
create proper turbulence (3500) through a 1/8 inch pipe waterline. The formula
can be adjusted for finding other items such as what Reynolds number should be
expected using specified waterline diameters and flow rates, or what temperature
water would be needed to create a specific Reynolds number. The important thing
to realize is that there are variable conditions under which the ideal Reynolds
number range of from 3500 to 7000 can be achieved. We should strive to maintain
a Reynolds number of 5000, if at all possible, to ensure that we are providing
proper heat transfer ability for the coolant being used to control the operating
temperature of the mold.
You can easily detect whether
or not a mold temperature is being properly maintained by noting the temperature
difference between water going in and water coming out. Contrary to popular
belief, there should not be more than a 10 degree (F) difference between the two
temperatures. If outgoing water is hotter than incoming water, it actually means
that there is still too much heat being retained in the mold and the water is
not bringing it out fast enough. An ideal condition is that the heat is being
removed as fast as it is being created, which would result in the water
temperature being exactly the same going in as coming out. While this may not be
entirely possible, there should be no more than a 10 degree F difference as
noted above. And, assuming waterlines have been designed for proper Reynolds
number, if the return water line is hotter it can be an indicator that a scale
build up is occurring in the lines, or some other item is plugging the flow.
- Determining Location Of
Waterlines
An easy statement to make is
that the waterlines should be located as close as possible to the surface of the
mold actually forming the molded product. While that is easy to state, usually
it is not easy to accomplish, if at all. The reason is that drilled waterlines
must follow straight paths, while most molded products have 3 dimensional
qualities and are not flat and straight. In many cases, drilled lines are placed
such that they surround the part as much as possible, but do not take the exact
configuration, as shown in the following drawing.
Improper
Waterline Pattern
The round-shape cavity is
surrounded by a square-shape waterline pattern. This is not efficient and will
cause uneven cooling in the molded part due to the uneven location of the water
being used to pull heat from the plastic. The uneven cooling will result in a
tendency for the flat part to warp and bow as some areas cool down quickly while
others cool at a slower rate. The following drawing shows a more accepted
waterline pattern for this product.
Acceptable
Waterline Pattern
Here, the coolant follows a
pattern that is much closer to the actual shape of the product being molded. In
order to create this pattern, however, a complicated system of drilled and
plugged waterlines must be created. This is expensive, and still does not form
an ideal pattern. A better pattern may be the one shown in the following
drawing.
Better
Waterline Pattern
In this case, the water flows
in a pattern that very closely matches the shape of the product being molded.
However, to incorporate this pattern requires a system of open-faced channels,
connected together, and sealed with "O" rings to eliminate leakage.
While this provides the most acceptable pattern, it is expensive to create and
requires constant maintenance to keep leaks from forming and damaging the molded
parts as well as the mold itself.
A further problem is that the
steel used for making the mold must contain the high pressure initiated by the
injection phase of the molding process, so the waterlines can't be too close to
the cavity or they will create a breakthrough of the cavity steel. A rule of
thumb suggests that waterlines be no closer than 1-1/2 times their diameter, but
a safer rule of thumb states they should be no closer than a full 2 diameters
from the cavity.
Waterline
Distance To Cavity
As we have shown earlier the
diameter is determined by what is required to provide the proper Reynolds Number
value, but that does not mean there should only be a single waterline. If depth
allows, additional layers of waterlines can be used.
Another factor to be considered
when locating waterlines is that there are other items that make up the
construction of the mold that may cause interference with the waterlines. For
instance, there are bolts that are used to hold the cavity blocks in place.
These come from behind the cavity blocks and might interfere with any waterlines
running under these blocks. Also, ejector pins for the part and for the runner
must travel through the B side of the mold, and these might interfere with
waterline locations.
Waterlines
And Interference Items
It is critical that the
mold designer lay these items out with two primary thoughts in mind: first,
locate the cavity blocks as close as possible to the center of the mold (to
minimize flow travel of the incoming plastic); and second, to locate waterlines
as close as possible to the contour of the cavity image. These two concepts must
be brought to bear on each other until a compromise is created which satisfies
both requirements.
- Bubblers And Cascades
Sometimes it is difficult to
get temperature control water located where it is needed. An example would be in
the center of a deep metal core such as those used for making waste baskets. In
those cases, specially designed components can be used. One popular component is
called a "cascade" and is commonly referred to as a
"bubbler", or sometimes a "fountain".
Water
Cascade (Bubbler)
In a bubbler, the cooling
medium (usually water) comes from the main cooling channel, enters at the bottom
of the bubbler, flows up through an inner tubular device, cascades inside the
unit, and flows down through an outer tubular device, exiting back into the main
cooling channel. This exiting water carries heat from the cascade unit into the
main cooling medium.
- Cooling Pins
Another device is known as a
"cooling pin" (sometimes called a "heat pin"). This unit
works on the conduction principle and is made from a thermally conductive
material such as beryllium copper. In the drawing that follows, the cooling pin
is connected to the metal molding surface and the base of the pin sits in the
main cooling channel. Heat is transferred from the plastic to the highly
conductive cooling pin. The cooling medium takes heat away from the cooling pin
by removing it from the base of the pin, to which point the heat has been
conducted. In some designs, the pin is hollow and contains a liquid or gas that
helps conductivity.
Cooling
Pin

Douglas M. Bryce
Chief Consultant
IPLAS
dbryce@iplas.com
http://www.iplas.com
020101B © 2001 IPLAS