Comparative Data Show Potential For Wheel Dryer To Replace Desiccant Bead Systems Now Dominant In Plastics
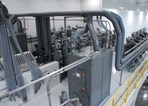
Baltimore, MD - Drying technology that has been widely and successfully used in other industries for more than a quarter century now promises to replace most conventional desiccant dryers employed to dry plastics resin, it was announced recently by NOVATEC, Inc.
Across a broad range of throughputs extending from 100 to 5,000 lb./hr.(45-2,300 kg/hr.), the NovaWheel desiccant wheel dryer outperforms conventional "dual-bed" or "twin-tower" desiccant-bead systems by margins great enough to enable wheel dryers to dominate new-dryer installations in the years to come, according to NOVATEC product sales manager Mark Haynie. He cited data developed by NOVATEC at its Drying Technology Center in Baltimore:
- 25% less energy consumption. In tests under controlled conditions, the energy cost per hour measured for the NovaWheel dryer was 35% less than a comparable NOVATEC-built dual-bed dryer for ABS and 14% less for polycarbonate (PC). Times required to reach acceptable moisture levels were similar. "The energy efficiency of the wheel dryer is the result of having three times the amount of pure desiccant per minute than in a twin-tower dryer," Haynie said. "On average we estimate that a new NovaWheel unit will use 25% less power than a conventional system."
- Up to 7.5 times longer desiccant life. Instead of being 100% pure, the desiccant beads in conventional dryers are only 70% desiccant, the other ingredient being a clay binder that holds each bead together. "The heating and cooling that beads undergo each time the desiccant is regenerated cause expansion and contraction that break down the binder, reducing drying efficiency, compromising dew point, and increasing energy consumption," Haynie said. "Ultimately the beads are reduced to useless dust and must be replaced with fresh beads while the dryer is off-line. This happens every two years in most cases. By contrast, NOVATEC guarantees a five-year working life for its desiccant wheel, and the lifetime can extend to as much as fifteen years."
- Up to 75% less floor space. The "footprint" of the NovaWheel dryer is only 25 to 35% of that for dual-bed dryers of comparable throughput. This results from the compact design of the wheel and the elimination of need for a second supply of desiccant.
Substantial Differences in Design and Operation between Old and New Dryers
Desiccant dryers pass hot air through a hopper full of resin to heat it and carry away moisture from the pellets to the desiccant bed, where moisture is adsorbed. The desiccant must be regenerated after each resin batch has dried, first by heating to around 350-400° F. (175-200° C) to drive off moisture, then cooling to recover full adsorption capacity.
Dual-bed dryers, today's workhorse systems, employ two desiccant beds to limit the batch drying process to the roughly four hours required to extract moisture, one bed being regenerated while the other is used for dehumidification. In wheel dryers, by contrast, a rotating wheel continuously puts dry desiccant into service while regenerating saturated desiccant in the same rotational cycle.
"Wheel dryers have been used for more than 25 years in the food processing, pharmaceutical, textile, and other industries and in recent years have become available from manufacturers of dryers for use by plastics processors," Haynie said. "We expect that the efficiency, consistency, simplicity, and compactness of the NovaWheel dryer will attract most of our customers looking to purchase new desiccant systems."
The key source of these advantages over conventional desiccant-bead systems is the design of the desiccant component in the NovaWheel dryer, according to Haynie. Inside the drum casing of the wheel is a tightly wound honeycomb that consists of a woven substrate to which 100% pure crystalline desiccant is bonded.
SOURCE: NOVATEC, Inc.