At NPE 2006: HDPE & LLDPE Resins Process Like LDPE
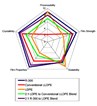
RAPREX (R) R-100 branched HDPE and RAPREX R-300 branched LLDPE exhibit the high levels of melt strength required for optimal blown film extrusion, blow molding, and thermoforming, according to product manager Ed Phillips. At the same time, he noted, the irradiation techniques employed by Sterigenics permit a high level of control over branching development that avoids crosslinking, preventing gel content and yielding PE that is completely recyclable.
"RAPREX resins enable processors to achieve greater profitability by increasing throughput rates and reducing scrap without compromising product quality and end-use performance," Phillips said. "Rheologically these materials behave like LDPE but retain the higher-performance physical properties of HDPE and LLDPE. The high strain hardening, high viscosity at near-zero shear, and good extensibility of these innovative resins are evidence of their stability and consistent performance in processes where melt strength is essential."
Phillips cited blown film as a case in point. "Historically, many blown film producers have blended LDPE and LLDPE to get the balance of processability and physical properties they need for manufacturing packaging films," he said. "RAPREX R-300 used alone provides higher blow-up ratios and improved gauge uniformity without dilution of physical properties."
The graph below provides an overview of the advantages cited by Sterigenics for RAPREX R-300 in comparison with other materials used for blown film, as well as improvements achieved by blending this innovative resin with conventional polymers.
SOURC: Sterigenics Advanced Applications